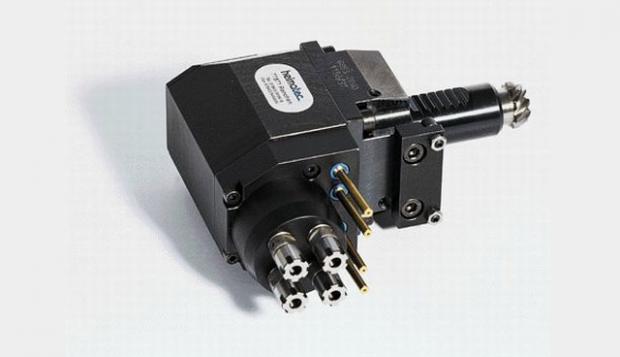
When any metalworking manufacturing facility, whether captive operation or job shop, makes the substantial investment in a new lathe, it is often looking for ways to streamline the manufacturing process. The smarter you are when choosing the live tools for your job, the more efficient the machine becomes. The key is to find a supplier of live tools that offers high-quality, high-performance products that will provide more flexibility on the first big job and into the future.
The first tool feature to consider is the output needed. Should that be standard ER output or quick change? Do you need coolant through the tool capabilities? Does the tool meet your requirements for precision and performance, including the necessary torque output to complement the machine? Are the tools designed according to the specifications of the lathe manufacturer?
When you look at an ER output, does it give you enough flexibility or do you need a more flexible machining system that will allow you to use the same tool for different applications? If more flexibility is required, then you may want to consider tooling with a system that features adapters for a variety of tools to avoid the cost of new complete toolholder assemblies for each tool needed. However, when you look at such systems, be sure they feature a rigid polygon drive system design to prevent power transmission and alignment issues. Such systems seem appealing, because the live tool stays in place and only the adapter and collet get changed out with each new tool. However, less-sophisticated though inexpensive systems will compromise the accuracy of your work. At that point, the few dollars saved will mean very little, compared to the resulting scrap and downtime.
If change-over time is critical, such as when working on a “family of parts,” the option of a true “quick-change system” might be more beneficial. Adapters can be set offline and ready to go for minimal change-over time.
When coolant-through tools are selected, it is imperative that you first check the machine specifications to be sure your tool is capable of handling the coolant pressure of the machine. In general, your internal coolant live tools should be able to handle 1,000 psi or more.
If your live tool is constructed with large, high-accuracy bearings, the tool will have excellent rigidity and premium cutting performance with minimal runout (0.0002" or 0.006 mm is a desirable goal). The bearings, combined with ground, paired and high-accuracy gears, make for tools that are consistent and long-lasting. Bore tolerance is absolutely key in maintaining proper bearing load and this factor should never be compromised.
In addition, you should consider the many applications that can be accomplished with the proper live tool. You can purchase speed increasers for higher rpm, gear reducers for added torque, adjustable angle tools for compound angles, multiple-spindle tools for additional capacity, or gear hobbing tools for spline or gear cutting. While most of those items are standard catalog devices, consider one more piece of advice: Never shy away from the custom tool, when appropriate and justified by the job you have in-shop today, as well as the ones you might have tomorrow. A good tooling supplier will work with you to produce custom tools at reasonable prices, but the supplier must be very reliable, so look for one with grinding, finishing and perhaps even heat treating in-house or very closely monitored, to do such work. Additionally, be certain the supplier has local support and tools can be repaired or reworked quickly and correctly.
The workpiece materials are always a driver. Those of you doing medical machining know this well. Buying a less expensive tool or one with fewer features to work cobalt chromium and titanium is a really bad idea, to be blunt.
On a practical level, always check the supplier for inventory and source of supply. Today, when your customers are demanding faster response times and more cost off-loading, you can expect the same from your tooling supplier. Likewise, application and engineering assistance should be available from local sources to support your tool choices.
The bottom line is the bottom line for most of us today. However, always consider the future jobs when purchasing tooling systems for your new and existing lathes. What might seem a bargain might not be, after the first big job is completed. |